Manufacturing Services
Having served the OEM market for many years, Modern Orthodontics is a leading manufacturer of all orthodontic parts including MIM parts, sheet metal parts and all type of wires. Some of the world's most prestigious OEM companies have selected MO as their manufacturing partner.
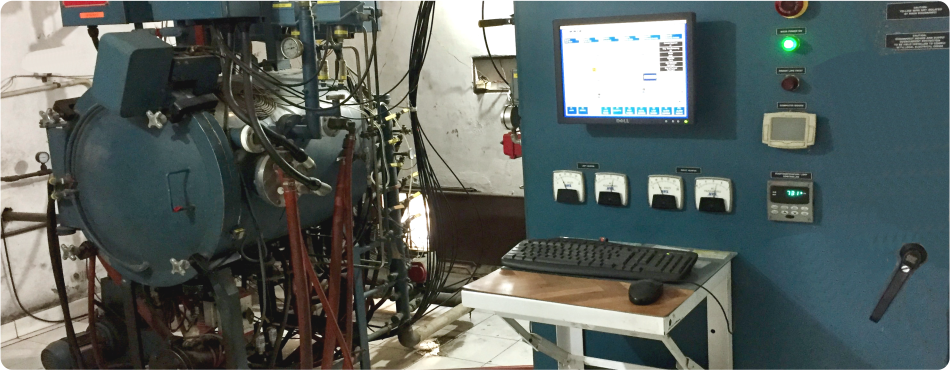
MO's skilled team of manufacturing specialists is here to serve you.
By partnering with MO, you'll have access to our expert engineering and design assistance, giving you the peace of mind that your job will be done right at a price you can afford. Our lead times, which are among the shortest in the industry, will ensure that your project is turned around as quickly as possible.
MO’s management team has extensive experience in mold making, MIM manufacturing, Sheet metal components and wire products - experience that will benefit you through higher quality parts that are produced on time. We operate under a single tier management system that allows us to provide our customers with quick response to their needs.
You as well are invited to take advantage of our expertise, without hidden adaptation costs. Our reputation is built upon a foundation of commitment to quality, unparalleled service, and on-time delivery.
What is Metal Injection Molding?
Metal Injection Molding (MIM) is a highly specialised process that combines the technologies of plastic injection molding and powder metallurgy to produce many of the intricately-shaped, highly accurate orthodontic parts made by MO
The MIM process consists of mixing fine metal powders with thermoplastic binders to form a feedstock which is injection molded. After this, thermoplastic "binders" are chemically or thermally extracted from the part so that the part can be sintered to high density. During the sintering process, the individual particles metallurgically bond together as material diffusion occurs to remove most of the porosity left by the removal of the binder. The sintering process shrinks the part, providing a net shape that can be used as-is or further worked to add additional features or improve tolerances. The result is a near full density, high strength metal component.
Benefits of the Metal Injection Molding Process:
MIM offers mechanical properties that exceed those available with plastic injection molded or die cast materials. Metal Injection Molding also provides a cost-effective, automated alternative to the labor-intensive investment casting process. With the ability to produce highly complex geometries, MIM is an effective alternative to complex machined components or intricate assemblies.
Metal Injection Molding is especially effective at producing small, complex components that require thin, uniform cross sections (up to .250 inch). Thicker sections are typically limited factors that include the high cost of the raw material, the difficulties involved in molding defect-free thick sections, and the ability to remove the binders effectively from the molded parts.
The economics of the MIM process favors higher annual part volumes, making it the perfect choice for orthodontic manufacturing. Although MIM can be a cost-effective solution for small, complex parts at lower volumes, the cost of molding tools discourages lower volume applications.
To ensure that the full benefits of the Metal Injection Molding process are best realized, MO considers the MIM manufacturing process during the initial design stage of the product.
The primary benefits of the MIM manufacturing process include:
Design Flexibility - By offering design flexibility similar to plastic injection molding, MIM enables the production of geometrically complex parts that cannot be produced using the conventional powder metal processes without secondary machining.
Intricate Details - MIM technology allows for intricate features such as dovetails, slots, undercuts, threads, and complex curved surfaces. MIM can also produce cylindrical parts with greater length-to-diameter ratios.
Reduced Assemblies - To minimize assembly costs, the MIM process can be used to combine two or more simpler shapes into a single, more complex component.
Reduced Waste/Machining - MIM's capability to provide net shape components eliminates many secondary machining operations.
Improved Physical Properties - MIM parts are typically 95% to 98% dense, approaching wrought material properties. MIM parts achieve greater strength, better corrosion resistance, and improved magnetic properties when compared to conventional powder metallurgy processes.
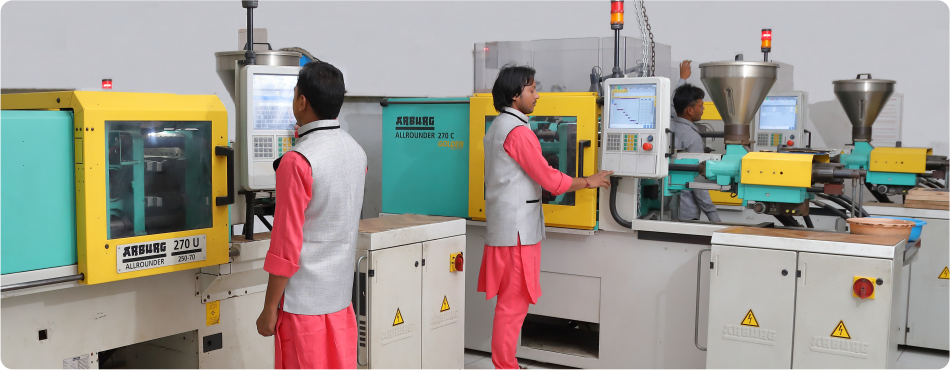
Process of Metal Injection Molding (MIM)
The MIM process includes the following steps:
Mixing - Metal Injection Molding feedstock begins with micron-sized metal particles. The metal powders are hot mixed with thermoplastics chosen to provide the necessary rheological properties for molding, mechanical properties for handling, and chemical and physical properties for ease of subsequent binder removal. Good feedstock formulations balance numerous conflicting cost and processing factors relating to both powder and binder selection.
Molding - Standard plastic injection molding machines are used to form Metal Injection Molding components. The feedstock is heated in the barrel to soften the powder/binder feedstock to a toothpaste consistency. This hot paste is injected into a closed mold cavity and cooled prior to ejection. Robotic pick-off is typically used to prevent handling damage.
Debinding - Once the part is molded, the thermoplastic binders used to help the powder flow into the die are no longer needed and must be removed. First, a portion of the binder is removed to open up a pore network within the part. The remaining binder is subsequently removed through the open pore network that has been created. This two-stage process removes the binder without creating internal cracks or voids within the part. There are several effective binder removal methods in commercial practice, both thermal and chemical, each with its own set of advantages and limitations.
Sintering - After the binder is removed, the parts are heated in a protective atmosphere to a temperature high enough to create metallurgical bonds between the powder particles and cause densification. This process typically relies on solid state diffusion and/or liquid phase formation to drive the densification process. The parts typically shrink 15 to 20 percent from the original die size during sintering to achieve final component density of 96 to 98 percent of full density. Optimum sintering temperature depends on the material, typically 2200°F to 2550°F (1200°C to 1400°C) for ferrous materials.
Nickel Titanium Wire Drawing
We are one of the few orthodontic manufacturers who have an in-house wire drawing facility. Our modern wire drawing shop can draw all Nitinol and Stainless-steel wires in-house. Modern Orthodontics Nickel Titanium wire is the result of years of research and advancement in several key areas of the material science over the period of years.
Nickel Titanium is an alloy which is complex to process and form. Very slight variations in a multitude of factors during manufacturing can alter the clinical performance of NiTi wires. MO has worked hard to achieve consistent force, elasticity and memory of each wire. The manufacturing processes some invented, some developed and others refined by MO to make NiTi distinct from all other NiTi archwires used in orthodontics. Only the scientific testing of a NiTi wire can determine its actual working characteristics. Modern Orthodontics NiTi archwires undergo intense scientific testing during the manufacturing process. Every wire undergoes a 100% final inspection before packaging.
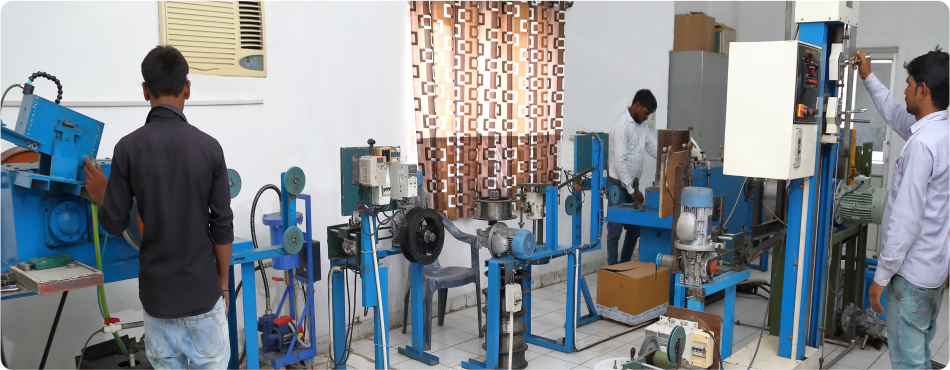
NiTi wire provide lower initial load forces and increased residual forces as full shape recovery progresses. Lower Loading Forces of Engagement result in easier wire deflection and delivery to bracket, less stress on bonds and increased patient comfort. Higher Residual Forces of Recovery gives full shape recovery, complete unraveling and archform development by staying active to the end.